Sampling Valve Control of a Diesel Engine
This use case was kindly provided by Embedded Solutions. For more information on MicroDAQ, check their presentation at ScilabTec 2015
It is a part of a research project on Diesel engine done by the National Institute of Maritime, Port and Aviation Technology from Japan.
Challenge
The quality of air-to-fuel mixture is of prime importance for effective combustion in Diesel engines. When it comes to qualitative measurement of mixture formation inside the combustion chamber, the crank angle resolved control of a high-speed gas sampling valve is of great importance. Usually, engines are equipped with a rotary encoder providing digital or analog signals about the top dead center position of a piston and the motion of a shaft. These two signals can be used for estimation of instantaneous angle position of the shaft and knowing the angle the sampling valve can be activated at the desired position with the desired period.

Solution
The four fast acting valves are used for gas sampling purpose. These valves are driven by the power module which accepts external control signal for activation of the valves. The microDAQ E2000 platform was employed to measure encoder signals, calculate instantaneous angle and send activation signal to the power module. Thanks to the flexibility of microdaq toolbox in easy integration of custom C/C++ code, the Xcos model was adapted for the purpose of current task. Finally, using the “Execution profiling” feature, the control model performance was confirmed up to 20 kHz sampling time, which is crucial for precise calculation of instantaneous shaft angle.
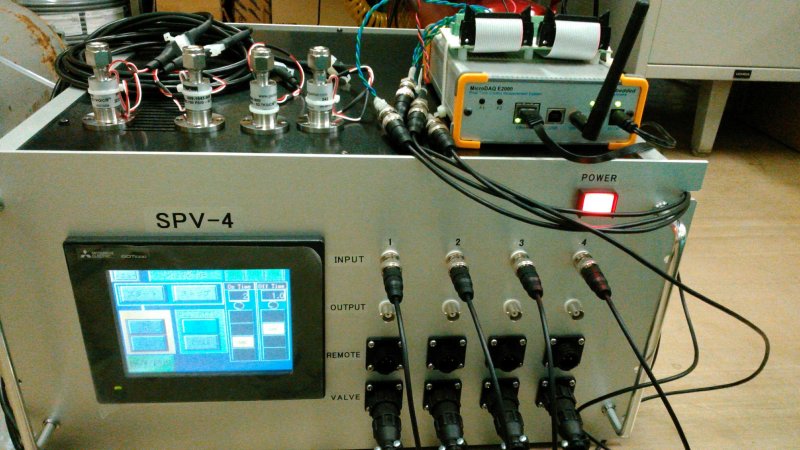